Working Principle and Process of Chemical Dosing Systems
By: Kate Nana
Post Date: May 14th, 2025
Email:Kate@aquasust.com
Post Tags: Dosing Systems, Working Principle and Process of Dosing Systems
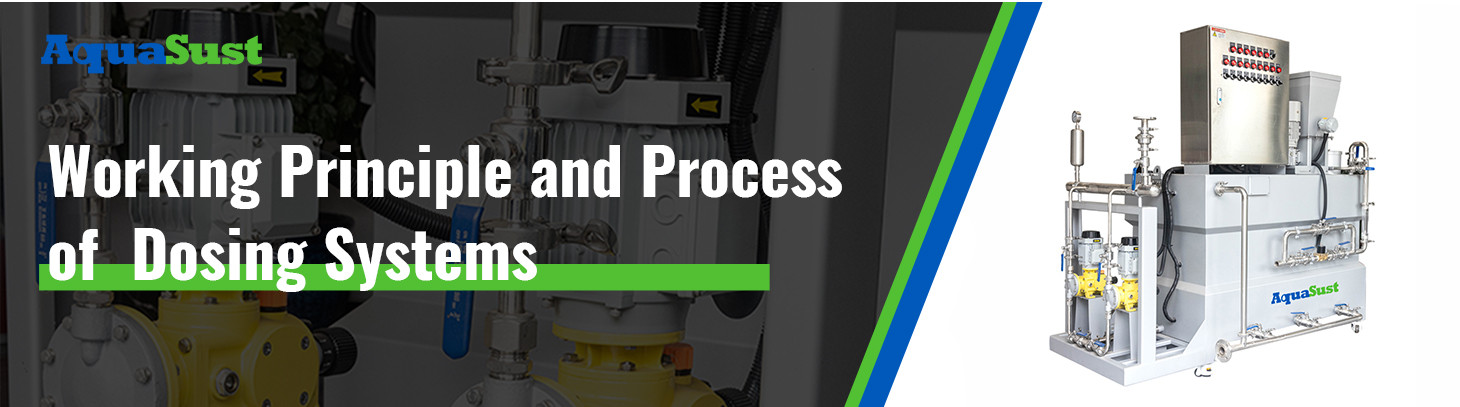
Dosing System
A chemical dosing system is an integrated equipment designed for the precise dosing, mixing, liquid transfer, and automated control of chemicals. It is widely used in circulating water systems requiring the addition of corrosion inhibitors, scale inhibitors, and biocides for water quality treatment. In water supply and wastewater treatment processes, various chemical agents—such as coagulants, flocculants, scale inhibitors, and disinfectants—are added to achieve water purification. These chemicals, in solid or liquid form, must be dissolved, diluted, and proportionally dosed to ensure efficacy. Thus, chemical dissolution and dosing systems are essential in water treatment engineering.
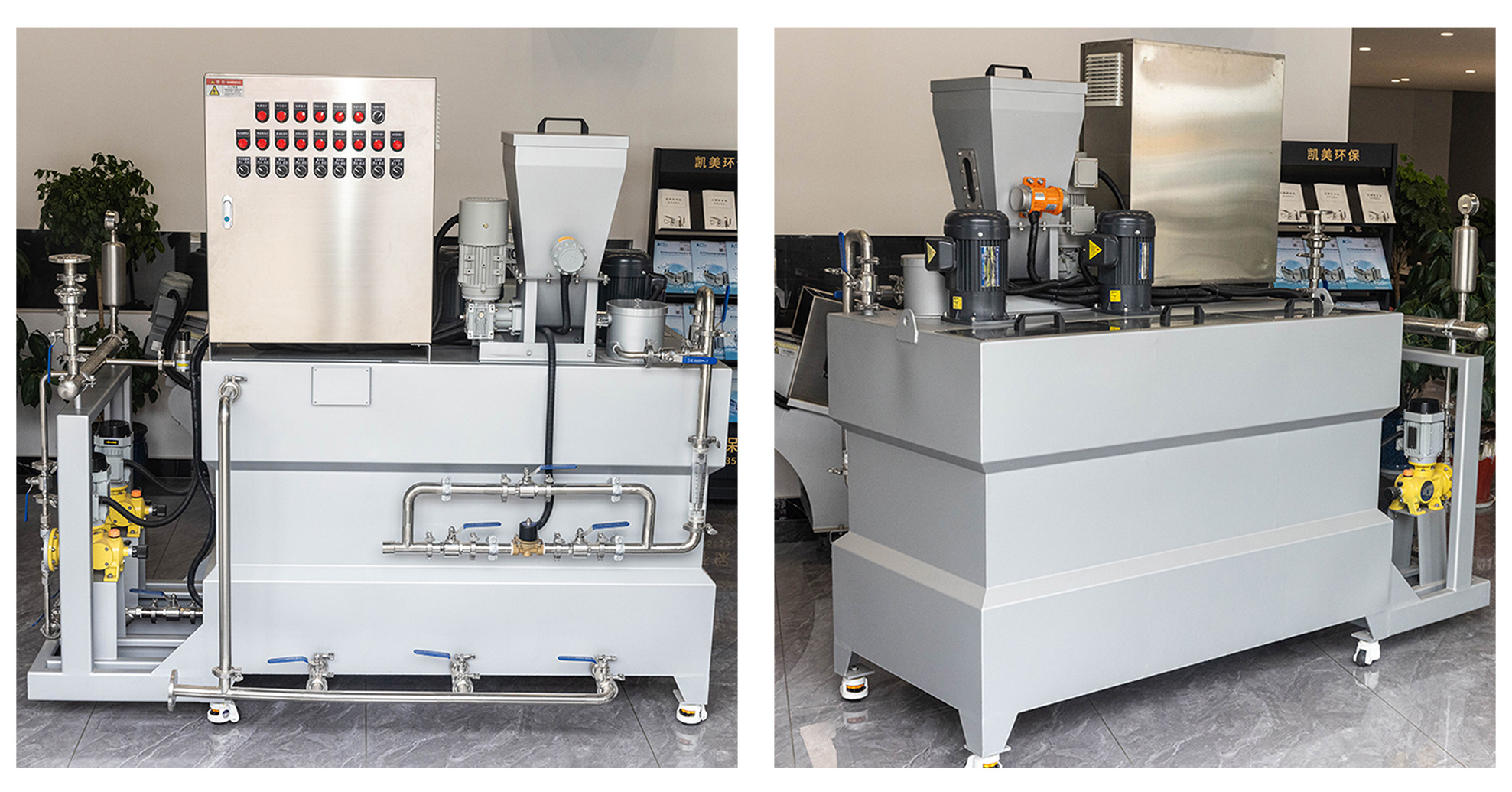
Applications
Primarily employed in power plants for boiler feedwater, condensate, circulating water, and wastewater treatment, these systems are also used in petroleum, chemical, environmental protection, and water supply industries. In wastewater treatment, they are utilized to prepare flocculant solutions, particularly in papermaking, industrial wastewater treatment, municipal sewage treatment plants, and drinking water facilities.
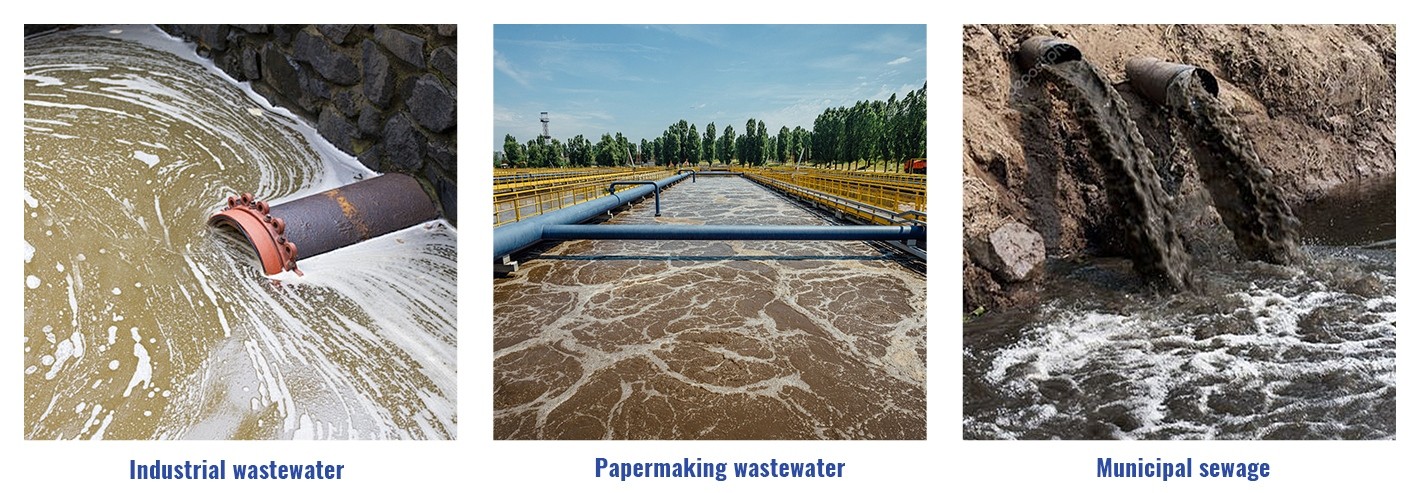
Working Principle
The dosing pump motor, driven by an AC frequency converter, injects chemicals into the liquid. A sensor detects the chemical concentration and transmits an electrical signal proportional to the concentration to a controller. The controller compares this signal with a preset value to generate a deviation signal. Through proportional and integral calculations based on process requirements, the controller sends the resulting output signal to the frequency converter. The frequency converter adjusts the motor’s power supply frequency, altering its rotational speed. This regulates the chemical injection rate, ensuring precise control of the dosing concentration.
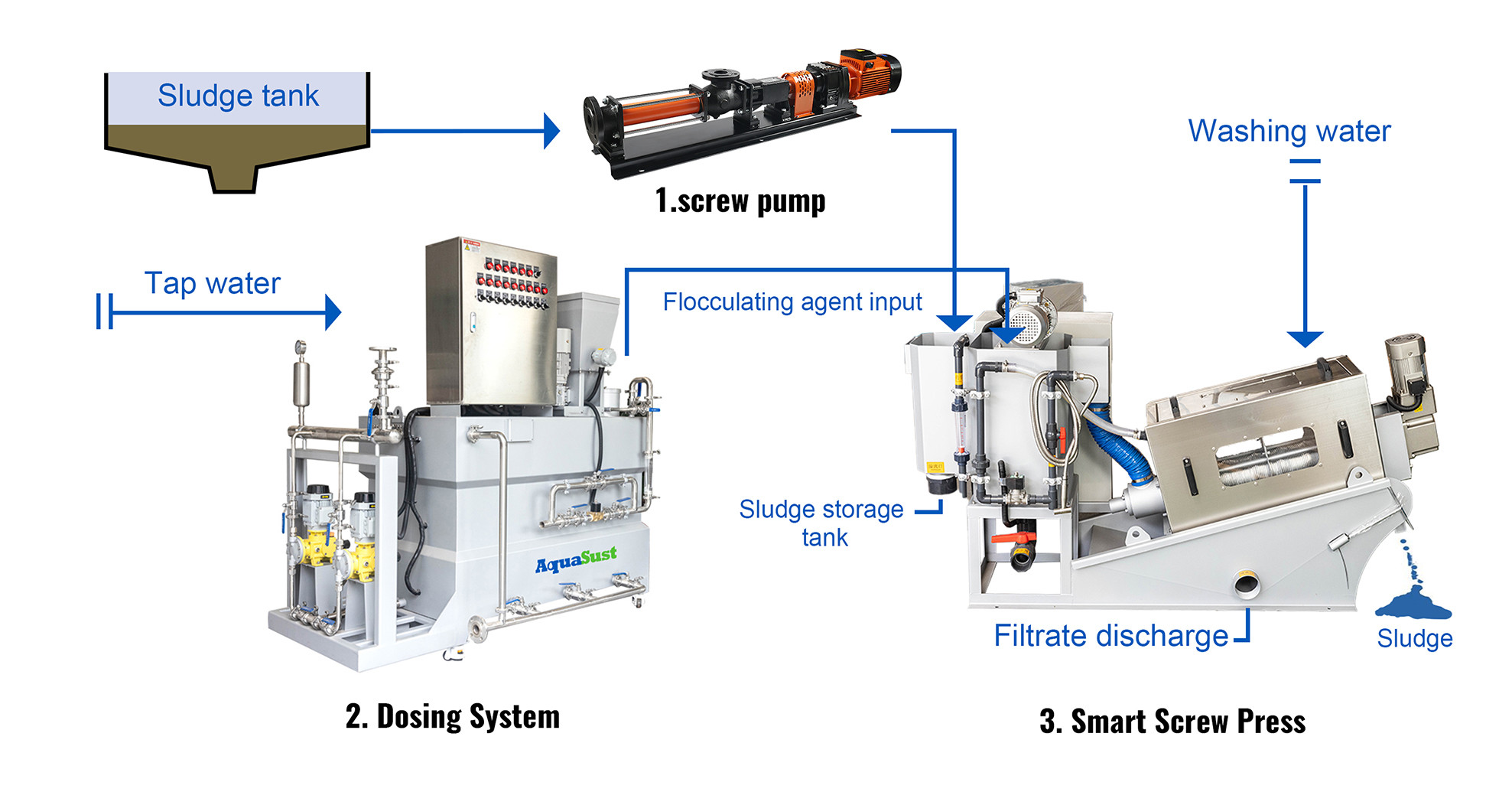
Process Flow
1. Under the control of an electrical cabinet, water and dry chemical powder from the hopper are fed into a dry-wet mixer at timed and speed-regulated intervals. The mixture is preliminarily blended and then injected into the main tanks of the automated dosing system.
2. The main tanks typically consist of three compartments: a preparation tank, a maturation tank, and a storage tank. Each tank is equipped with an agitator, and compartments are separated by baffles lower than the tank height. This allows the chemical solution to overflow sequentially after thorough mixing in each stage.
3. Water and chemicals are fully homogenized through agitation across the three tanks, gradually forming the desired solution, which is stored in the storage tank. Using screw pumps and pipelines, the solution is then delivered to target equipment requiring chemical dosing.